Nestled in the woods, a mile off Pickard Road in Canterbury, sits a 40-acre farm where Barbie Tilton lives and cares for dozens of animals.
After a career spanning 33 years in information technology, Tilton left the industry to invest in alpacas. Not only do the alpacas require less work than the horses and cows she grew up caring for, but Tilton explains that alpacas are more profitable than many other animals, through avenues of breeding, shearing and showing.
“Alpacas are an investment, like a home,” she continued. “You buy them, you sell them and they depreciate over time.”
Nearly 24 years ago, she started Someday Farm with her late husband on a plot of land abutting her current farmhouse. Experienced in working with farm animals since her youth, Tilton has made her mark in the New Hampshire alpaca industry, and is known for her pristine female alpacas and fleece. Prior to 2019, she owned 70 alpacas, draft horses, cows, goats and hundreds of fowl.
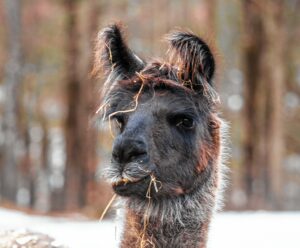
Barbie Tilton lives on a 40-acre farm in Canterbury and invested in alpacas a farm animal that was less work than the horses and cows she grew up tending.
Now, she owns nine female – hembra – alpacas that are bred independently, sheared annually and are free to roam and graze with their herd. Of the nine, two are crias – babies. Though they are often independent from birth, they typically stay close to their mothers for the first few months of their life and begin to wean at around six months.
Alpacas are profitable in the fleece produced, but shearing is also necessary for the animal’s hygiene, comfort and overall health. Alpacas are unable to shed fleece themselves, so it’s necessary for people to shear them annually after the winter months. If shearing is neglected, they can overheat and develop skin problems or illnesses that could kill them.
For Tilton, this shearing process takes place on the first Saturday of May every year, when she brings in a local shearer to strip the alpacas of their fleece – usually several inches in length by that point.
The alpacas are shuffled into the barn, locked in, and led one by one into the center of the barn where they are secured by their hooves and brought to the ground on a thin sheet or tablecloth. The ropes around their hooves are tightened and the animal is pulled taught while the shearer glides the blade evenly over the stomach and sides, rolling the animal over as the fiber detaches from the animal in one fluid movement.
Then, the shearer works down the legs and the tail, up over the chest and neck, and finishes with the top of the head. The fiber is then collected, filtered of any dust and vegetation, weighed and separated by color, and packaged for distribution to mills where the fiber is processed, or to local artisans who make their own yarn.
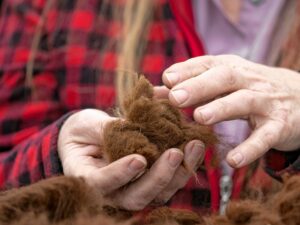
Barbie Tilton lives on a 40-acre farm in Canterbury and invested in alpacas a farm animal that was less work than the horses and cows she grew up tending.
Nearly 24 years ago, she started Someday Farm with her late husband on an abutting plot of land to her current farmhouse and barn thats since been sold. Growing up taking care of farm animals her entire life, she made her mark in the New Hampshire alpaca industry for her pristine females and fleece. Up until 2019, she owned 70 alpacas, draft horses, cows, goats and hundreds of foul.
“It takes about 10 minutes to shear one alpaca,” Tilton said. “It can be made into wool with carting paddles or spun on spinning wheels to make yarn that can be sold in bundles or used to knit scarves, mittens, hats, socks or rugs.”
Tilton used to shear the alpacas on her own and often spun her own wool, but the process has become difficult on her body as she’s aged. She further explained that hiring a shearer is easier, more time efficient, and less stressful for the animals.
When breeding alpacas for shearing, Tilton looks for certain traits in the animals; the length of their fiber, their alignment, profile, posture, temperament and level of care for their offspring.
If, for example, a female alpaca has thinner fiber around her hooves, a breeder would look to mate her with a male that has thicker fiber around his hooves to fill out their offspring and upgrade the female, Tilton said.
“The length of their fiber is important,” she continued. “You want it to be three inches at the time of shearing, and we will not continue to breed the animal if it doesn’t meet the breeding requirements to make a good shearing alpaca.”
If the fiber is not three inches in length, Tilton said, mills won’t process it and buyers will have limited options for their craft, like rugs. Often, Tilton has to collect fiber for several years before it can be sold to a mill.
The first cut, which is frequently reserved for scarves, hats, sweaters, socks and mittens, is the most acquired fiber and is taken from the belly, neck and haunches of the animal. The rest, from the bottom of the legs to the tail, is processed for knick knacks, hobby crafts and rug making, where the fiber doesn’t need to be spun into a wool or a yarn.
Tilton explained that the more the fiber is processed, the more profitable it can be for a breeder. For example, a 10 pound bag of fiber from one animal can be sold raw to a mill for $50, or spun into five spools which can be sold for $20 each, making an additional $50 for the farmer. Once in the yarn stage, the wool can be made into garments and further sold, increasing the profit from $50 at the raw stage to hundreds when fully processed.
“The more you process it, the more you can make off the animal and some animals, with the sale of their babies, will pay for themselves during their lifespan,” Tilton continued.
To purchase fiber or yarn from Someday Farm, visit Tilton’s Facebook page for upcoming farmer’s market and open house dates: facebook.com/somedayfarmnh.